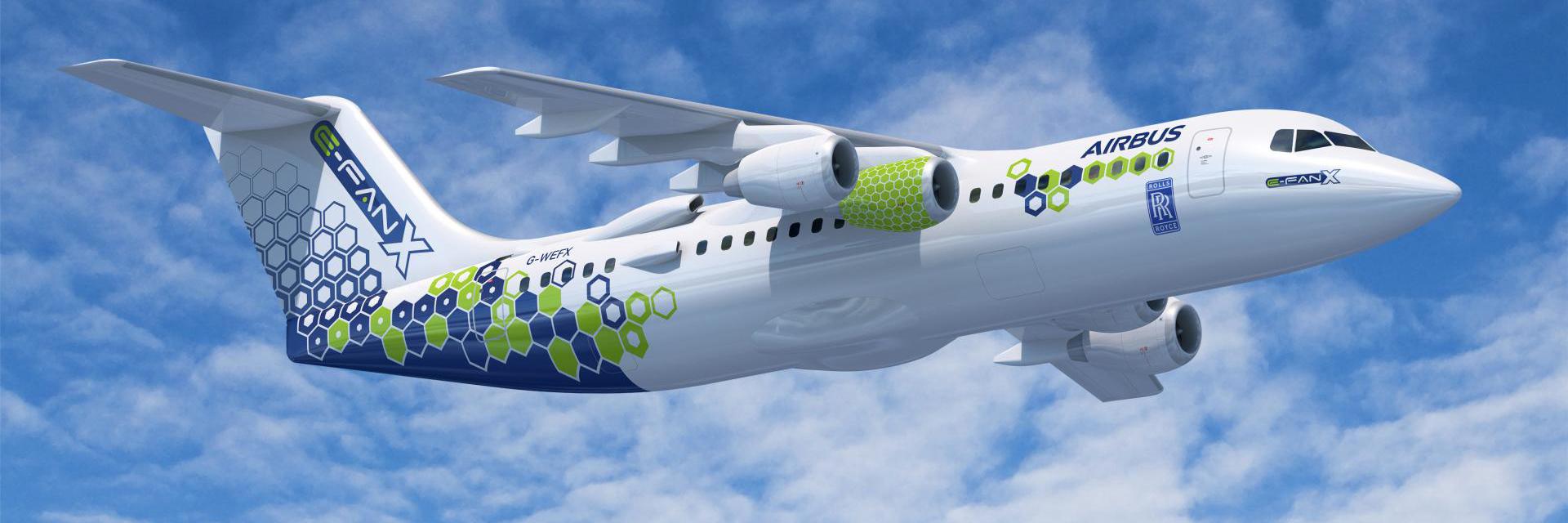
El sector aeroespacial europeo emplea habitualmente materiales compuestos de plástico termoestable —también conocidos como composites basados en resina epoxi—, de bajo peso y alto rendimiento, en muchas aplicaciones. Sin embargo, estos materiales no son tan resistentes a las altas temperaturas como los componentes metálicos de las aeronaves, lo cual puede comprometer la seguridad en situaciones en las que se alcancen temperaturas extremas. Con el objetivo de mejorar el comportamiento de los actuales composites termoestables ante las exigencias de la cada vez mayor electrificación de la aviación, el equipo de investigación HITCOMP (High Temperature Characterization and Modelling of Thermoplastic Composites), coordinado por la Universidad Carlos III de Madrid (UC3M) ha planteado una alternativa: el uso de nuevos materiales termoplásticos basados en resinas PAEK.
Las resinas PAEK (siglas en inglés de poliariletercetona) constituyen una familia de plásticos semicristalinos en la que se forman cadenas de anillos de benceno con dos sustituciones (grupos arilo, fenilenos) unidos por eslabonaes que contienen oxígeno: alternativamente éter (R-O-R) y cetona (R-CO-R). Su temperatura de procesamiento está en el rango de 350-450 ºC. Suelen emplearse en impresoras 3D. Esta técnica ya tiene amplio uso aeroespacial.
«El sector aeroespacial está en proceso de transición hacia un avión más eléctrico. Esto implica más fuentes de calor y eventualmente de fuego, aumentando el efecto térmico sobre la estructura. En este marco, nuestro proyecto tiene como objetivo establecer una metodología innovadora que permita una caracterización de los termoplásticos que implique menos recursos y mejore la predicción de su comportamiento y resistencia cuando se someten a cargas mecánicas o a eventos de fuego y altas temperaturas».
Fernando López, investigador principal y coordinador del proyecto HITCOMP. Departamento de Física de la UC3M
En el transcurso del proyecto HITCOMP se ha demostrado que los componentes fabricados con una base termoplástica son más eficientes, desde el punto de vista de sus propiedades térmicas, que los composites termoestables. Una propiedad conocida que los hace muy útiles es que se pueden volver a fundir, moldear, procesar y reciclar, sin necesidad de ningún proceso de curado adicional para endurecerse y fraguar. Además, son materiales más versátiles, baratos y ecológicos que los composites termoestables convencionales y tienen una vida útil mayor, gracias a su alta capacidad de recuperación —pueden reciclarse o repararse con mayor facilidad— y su resistencia a la fatiga —el desgaste por uso— y la corrosión. La introducción de estos materiales supondría contar con aviones más seguros y ligeros, que consuman menos combustible, aprovechen mejor la energía y reduzcan sus emisiones.
Para sacar el máximo partido a los termoplásticos en la industria aeroespacial, dada su tendencia a fundirse y deformarse a altas temperaturas, hay que caracterizar su comportamiento cuando son sometidos a sobrecalentamientos, al fuego y a cargas mecánicas. Para conseguir mediciones precisas y no intrusivas de la temperatura real de los materiales durante las pruebas de fuego, el proyecto HITCOMP ha desarrollado un laboratorio de ensayos con técnicas novedosas de termografía infrarroja. El objetivo final es realizar ensayos virtuales de los termoplásticos y comparar sus prestaciones en aplicaciones reales con las de los composites termoestables convencionales.
Las medidas obtenidas mediante termografía infrarroja permiten realizar simulaciones por ordenador, que virtualizan los ensayos para seleccionar este tipo de materiales en la industria aeronáutica. Se espera que con su aplicación «disminuya notablemente el número de ensayos de validación, que son obligatorios y que encarecen y retrasan enormemente la aprobación de este tipo de materiales en la industria». A día de hoy, ya se han transferido a Airbus los modelos y equipos infrarrojos para que pueda estudiar su aplicación industrial.
Durante el proceso de investigación, el equipo también ha desarrollado un nuevo método —inspirado en los resultados previos del Laboratorio de Sensores, Teledetección e Imagen en el Infrarrojo de la UC3M (LIR-InfraRed LAB)— que permite utilizar estas técnicas de imagen infrarroja para determinar, a distancia y sin contacto, las propiedades térmicas de estos materiales.
Sobre el autor: César Tomé López es divulgador científico y editor de Mapping Ignorance