mantenimiento
Another flaw in the human character is that everybody wants to build and nobody wants to do maintenance. (Otra falta de la condición humana es que todo el mundo quiere construir, pero nadie quiere hacer el mantenimiento.)—Kurt Vonnegut
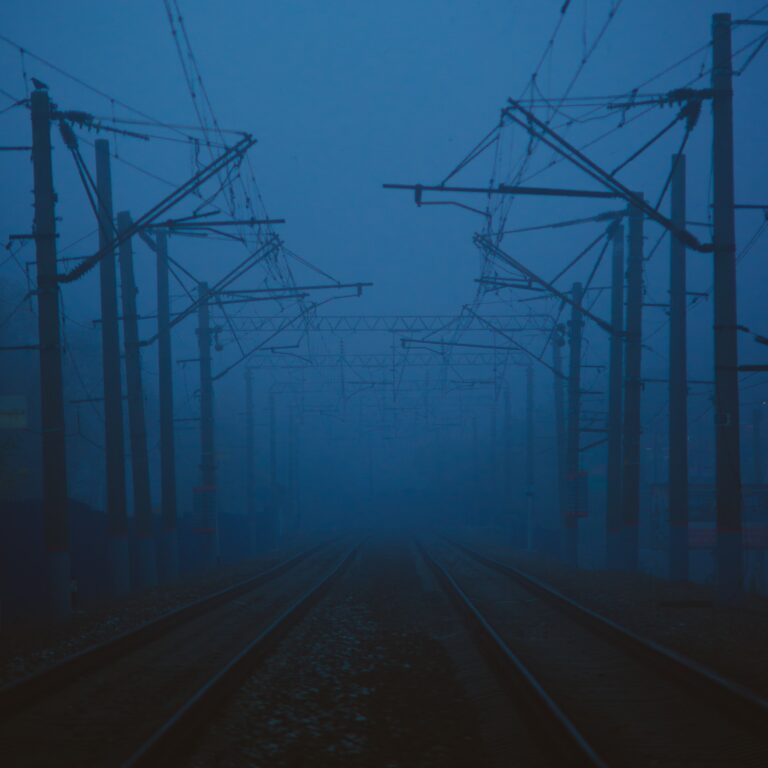
El mantenimiento es el conjunto de procesos necesarios para conservar la funcionalidad de cualquier sistema tecnológico en su nivel de diseño. Como todo proceso industrial, el mantenimiento tiene un coste asociado en capital, trabajo y huella medioambiental. Además, el mantenimiento lleva aparejado cierto nivel de indisponibilidad de los sistemas mantenidos. Estos periodos de parada o funcionamiento degradado suponen pérdidas que se pueden contabilizar en el propio proceso de mantenimiento. Reducirlas al mínimo imprescindible es un reto interesante, en el que juegan un papel fundamental las políticas de mantenimiento.
Al igual que los elementos materiales que comprenden toda tecnología, las políticas de mantenimiento también han experimentado una evolución con el tiempo. La primera y elemental es «cuando algo se rompe, se repara», también llamado mantenimiento correctivo. Esta aproximación, por sí sola, es inviable cuando tratamos con sistemas de los que depende la seguridad de las personas. Pronto se percibió que la indisponibilidad del sistema afectado, desde la avería hasta su puesta en funcionamiento, suponía por sí misma una fuente de costes considerable. Esto aparejó la creación de la política «revisamos el sistema a intervalos regulares», o mantenimiento preventivo. El objetivo es «cazar» los fallos antes de que sucedan, algo más fácil de decir que de hacer y que supone de por sí toda una nueva disciplina de la técnica.
Naturalmente, los fallos aún ocurren, ora porque escapen a los mecanismos de detección cuando aún son «prefallos», ora por puro azar. Un intervalo de inspección muy pequeño detectará un número creciente de fallos en desarrollo, y viceversa para tiempos crecientes. El propio acto de la inspección tiene un coste. Esto introduce su frecuencia en la fórmula del objetivo que deseamos optimizar. La práctica totalidad de los mantenimientos son todavía una combinación, ajustada para buscar un coste mínimo a mano o mediante herramientas estadísticas sencillas, de prevención y corrección.
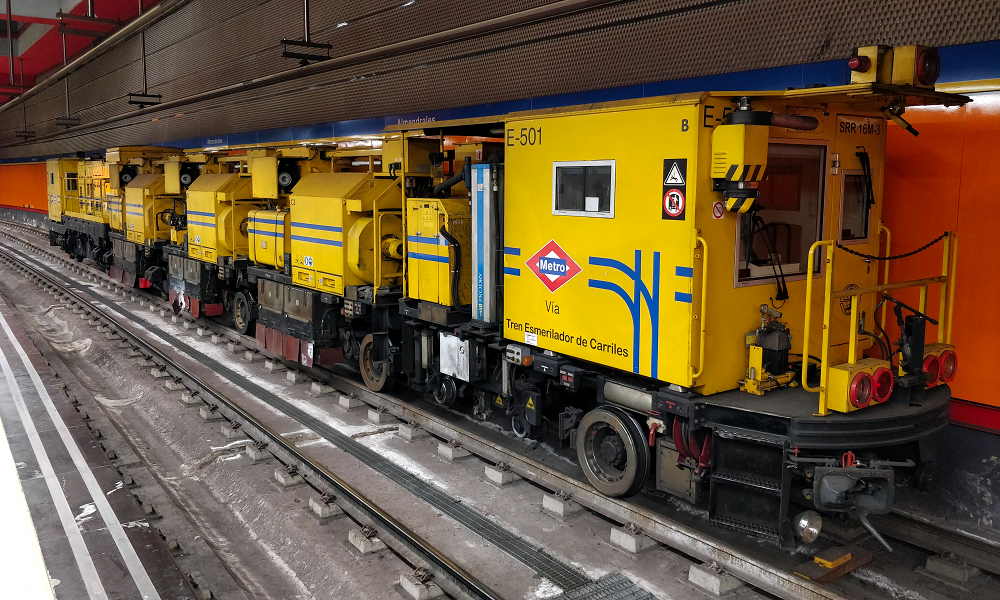
Un mundo ideal
Dos tipos de avances tecnológicos han permitido soñar con una política ideal, que podríamos denominar «cambiamos la pieza justo antes de que falle», o mantenimiento predictivo. Si, de algún modo, logramos retrasar las acciones de mantenimiento hasta un momento arbitrariamente cercano al del fallo, pero siempre anticipándolo, habremos eliminado la indisponibilidad por avería a la vez que espaciamos al máximo las intervenciones. El coste teórico de este mantenimiento es, por tanto, el mínimo posible para nuestro nivel de servicio deseado. ¿Cuáles son los avances que habilitan este salto conceptual?
En primer lugar, la disponibilidad masiva y barata de potencia de cálculo. Los ordenadores actuales son capaces de simular sistemas físicos de gran complejidad. Aunque estimar las solicitaciones sobre una catenaria flexible requiere realizar cálculos mecánicos, eléctricos y térmicos de forma simultánea, esto está al alcance de computadoras con un precio razonable.
Pero los cálculos no lo son todo. Cualquier sistema físico más complejo que la proverbial vaca esférica carece de soluciones analíticas. Es decir: no existen ecuaciones sencillas y fáciles de calcular que lo representen. Hay que recurrir a métodos numéricos iterativos: un conjunto de fórmulas más o menos simplificadas que se ejecuta, recurrentemente, para momentos sucesivos de un tiempo en el que consideramos una subdivisión básica. No importa cuál: horas, segundos, milésimas de segundo. Cualquiera de ellas establecerá una contrapartida entre la precisión obtenida y el tiempo real en el que obtendremos respuestas. Disponer de ordenadores más rápidos no evita la existencia de este dilema, solo lo desplaza a un punto de equilibrio diferente. Además, el tipo de matemáticas que suele ser necesario resolver provoca que doblar la potencia de cálculo no suponga, en general, dividir por dos el tiempo de proceso o multiplicar por dos la precisión, sino considerablemente menos. Cada iteración calculada tendrá un error que irá, inevitablemente, a alimentar la entrada de la siguiente. En un número de ciclos que depende de cada sistema simulado, la deriva de las respuestas respecto de la realidad será tan grande como para hacer inútil todo el ejercicio.
Es aquí donde entra en juego el segundo avance: los sensores. Hoy es mucho más sencillo y barato conocer valores para las variables de estado de un sistema real gracias a la miniaturización de la electrónica. Quien mide, sabe (aunque medir también es un arte de la ingeniería, sujeto a sus propios balances entre precisión y exactitud). Si en una simulación introducimos periódicamente correcciones derivadas de lecturas de sensores en un sistema real, podemos controlar el error y, por tanto, la deriva.
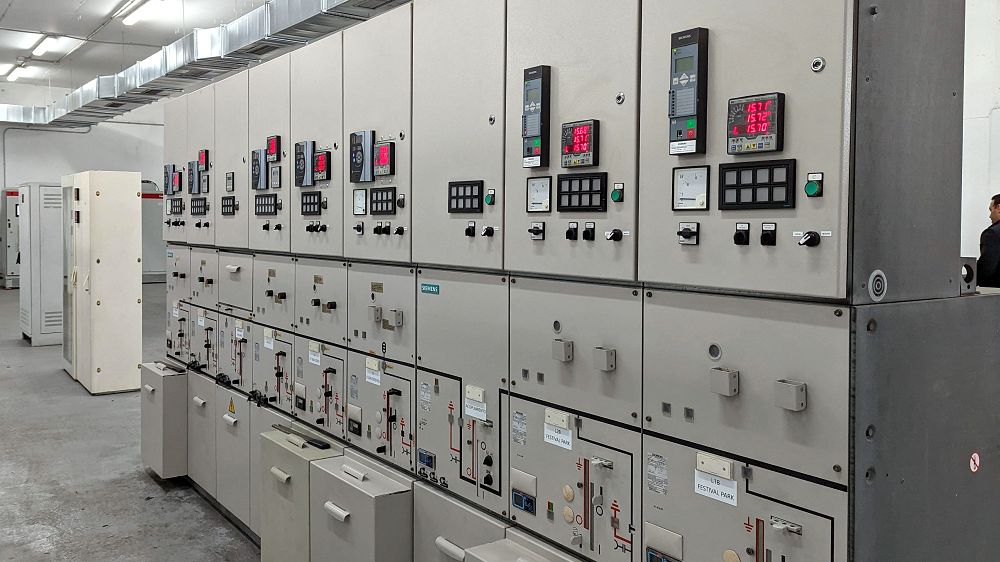
«Mellizos digitales»
Lo que tenemos entre manos pretende ser un «gemelo digital»: un sistema simulado capaz de ofrecer respuestas concretas ante todo tipo de cuestiones. ¿Qué efecto tendría sobre la catenaria duplicar el tráfico de trenes? Podríamos «copiar y pegar» series de datos registrados en los sensores para hacernos una idea. ¿Y si queremos conocer el efecto de un aumento de la temperatura en un verano particularmente duro? Podríamos simular la dilatación extra sobre el metal.
Ni que decir tiene que un auténtico gemelo digital es una quimera, tanto por las limitaciones de los métodos y la capacidad de cálculo como por las imprecisiones —inevitables— cometidas por los sensores. O por su ausencia, ya que no será económicamente viable llenar de artefactos de medida toda la infraestructura. Medio en broma, podríamos decir que lo que obtendremos de la fusión de simuladores físicos y sensores será un «mellizo digital». Algo razonablemente parecido al sistema real. Lo suficiente como para poder hacer predicciones fiables sobre su rendimiento y sobre las diferentes necesidades del mantenimiento. Esta es la teoría, pero ¿y la práctica?
En una instalación industrial genérica, una vez determinados los puntos de medida necesarios, debemos garantizar tanto la alimentación eléctrica de los sensores como su conectividad. Para lo que podríamos llamar «instalación concentrada», esto no es un problema serio. La alimentación está garantizada por una red de distribución de baja tensión convencional. En lo que respecta a la conectividad, podremos encontrar alternativas de todo tipo, inalámbricas y cableadas.
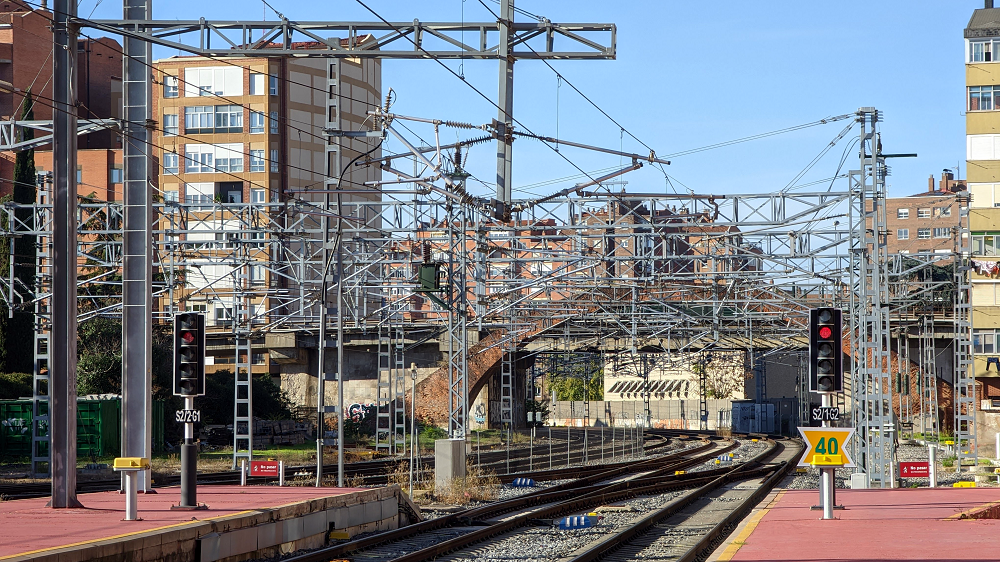
El problema de las instalaciones lineales
Pero la catenaria no es una instalación industrial concentrada: es una instalación lineal distribuida a lo largo de decenas, centenares, miles de kilómetros de red férrea. A pesar de que la catenaria transporta energía eléctrica, lo hace en unas condiciones en las que resulta particularmente oneroso transformarla entre su forma de consumo para el ferrocarril (en España, corriente continua a 3 kilovoltios o alterna a 25 kilovoltios) en una alimentación adecuada para los sensores y su circuitería asociada, generalmente 12 o 24 voltios en continua. Este problema se puede solventar, evitando kilómetros de red de distribución en baja tensión, mediante el uso de placas fotovoltaicas y baterías.
Los problemas de conectividad pueden soslayarse con el uso de la red celular 3G/4G, y si la cobertura resulta ser defectuosa, con agregadores y radioenlaces punto a punto u otras alternativas. Las redes específicas de baja potencia y largo alcance, como LoRaWAN o SigFox, diseñadas específicamente para ofrecer conectividad a sensores son interesantes siempre que la cantidad de datos a transferir por unidad de tiempo sea lo suficientemente pequeña; la experiencia muestra, sin embargo, que esta suposición resulta ser problemática para un buen número de prototipos de sensores asociados a la operación ferroviaria. La solución, el despliegue generalizado de las nuevas redes celulares 5G y sus sucesoras (6G está a la vuelta de la esquina), es cuestión de tiempo. A esto nos referimos los ingenieros de teleco cuando hablamos de «la Internet de las Cosas».
Suele decirse que, sin salir del planeta, los requisitos más estrictos de resistencia y durabilidad frente a los elementos están en el entorno militar, y justo después en la industria del transporte, donde la ferroviaria destaca por méritos propios. El ferrocarril tiene instalaciones extendidas a lo largo de centenares de kilómetros, expuestas a la intemperie, cruzando estepas, desiertos o selva, bajo temperaturas extremas y variables, en ambientes húmedos, salinos o contaminados por partículas en suspensión, con poca o ninguna vigilancia activa. ¿Cómo lograr hacer de una instalación como la catenaria una infraestructura monitorizada del siglo XXI?
Del mismo autor:
Los límites del Hyperloop
El camión solar: ¿una posibilidad real?
Sobre el autor: Iván Rivera es ingeniero especializado en proyectos de innovación de productos y servicios para ferrocarriles.
La catenaria al suelo, otra vez – brucknerite
[…] Rivera Rodríguez, Iván. «La catenaria: una introducción a su mantenimiento (2/4)». Cuaderno de Cultura Científica, 29 de junio de 2023. https://culturacientifica.com/2023/06/29/la-catenaria-una-introduccion-a-su-mantenimiento-2-4/. […]